X-Ray Inspection
Home / X-ray Inspections
Inspection
X-ray inspection of aluminum castings is one of the most effective techniques to ensure casting quality and detect defects such as porosity or blowholes, which could compromise the product’s reliability. Externally, a part may appear flawless, but hidden inside, there can be defects that are invisible to the naked eye. This is particularly critical in industries where structural integrity is essential, such as automotive, aerospace, or medical sectors.
Factors influencing casting defects
The formation of defects inside an aluminum casting can depend on various factors, including:
•Casting temperature: If the aluminum is not poured at the correct temperature, voids or air bubbles can form in the solidified metal.
•Solidification speed: Too fast or too slow solidification can cause microvoids or other imperfections.
•Alloy composition: The quality of the aluminum alloy used plays a crucial role. An unbalanced mixture can lead to solidification defects.
•Contaminants: Impurities or inclusions can cause blowholes and porosity.
•Casting technique: The casting method used, such as gravity casting or die casting, can influence the formation of internal defects.
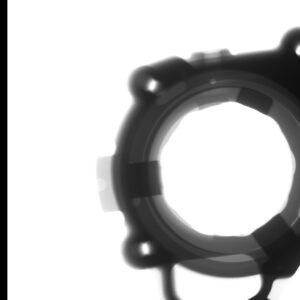
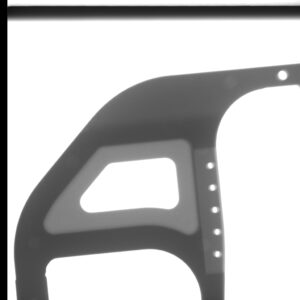
The effectiveness of X-ray inspection
With X-rays, it is possible to examine not only the surface but also the interior of an aluminum part. This technique allows for:
•Identifying hidden porosity.
•Detecting the presence of air bubbles or other structural defects.
•Ensuring the part meets stringent safety standards.
In fields like automotive, an unchecked part could lead to severe structural failures, causing mechanical breakdowns or accidents. Imagine, for instance, a suspension arm in a sports car failing due to a small, undetected porosity. Or, in aerospace, a tiny blowhole could reduce the strength of a critical component, leading to catastrophic consequences.
Concrete examples
- Automotive: In an engine, an aluminum part that is not properly inspected might have internal porosity, which under stress, could lead to sudden failure. This could result in engine breakdown or, worse, an accident.
- Aerospace: In the production of aircraft parts, even the smallest defect can compromise structural integrity. X-ray inspection ensures components are free of internal flaws, reducing the risk of aviation accidents.
- Medical: In medical devices made from aluminum, such as implants or surgical instruments, an undetected internal defect could lead to failure, with disastrous consequences for patient health.
Without X-ray inspections, hidden defects can turn into major problems in the long run. This is why their application is critical to ensuring that parts are not only perfect on the outside but are truly flawless inside as well.