Mold Design and Creation
Home / Mold design and creation
Importance of mold design
Mold design and creation are fundamental steps in the casting process, playing a critical role in determining the quality and functionality of the final product. A well-designed mold ensures that molten metal flows evenly, solidifies properly, and meets the desired specifications without defects. Whether it’s for aluminum casting or other types of metals, the precision in mold design significantly impacts the efficiency and cost-effectiveness of the manufacturing process.
Summary
1. Flow control: One of the key objectives of mold design is to control the flow of molten metal. The mold must guide the metal into every cavity and intricate detail without creating turbulence, which could lead to defects like porosity, air bubbles, or cold shuts. Proper design ensures that the metal fills the mold uniformly, reducing the chances of unwanted voids or weak points in the casting.
2.Solidification management: The way metal cools and solidifies within the mold is critical for preventing shrinkage or internal stresses that could compromise the structural integrity of the part. By designing molds with the right thermal properties and cooling channels, manufacturers can control how quickly different sections of the casting solidify, ensuring uniformity and reducing the likelihood of defects.
3.Precision and accuracy: A well-designed mold allows for high precision in the final dimensions of the casting. This is particularly important when producing parts that must meet tight tolerances, such as engine components or parts for aerospace applications. Poor mold design can result in dimensional inaccuracies that require costly post-processing or even render the part unusable.
4.Complex geometries: Modern casting often requires creating parts with complex shapes and intricate features. Mold design must account for these complexities, ensuring that the mold can handle these geometries without introducing flaws during the casting process. Features like undercuts, sharp corners, and thin walls all require careful attention during the mold design phase.
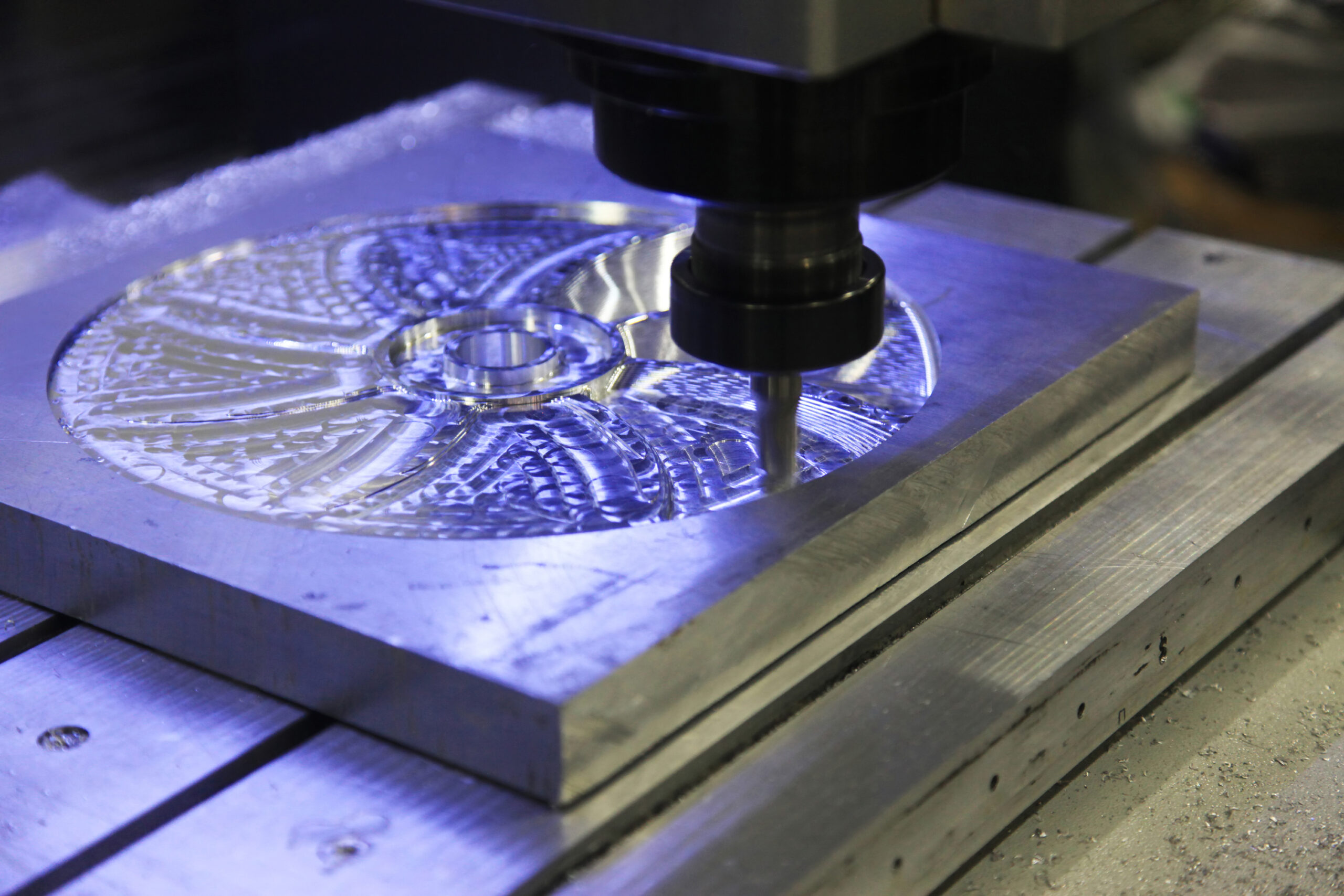
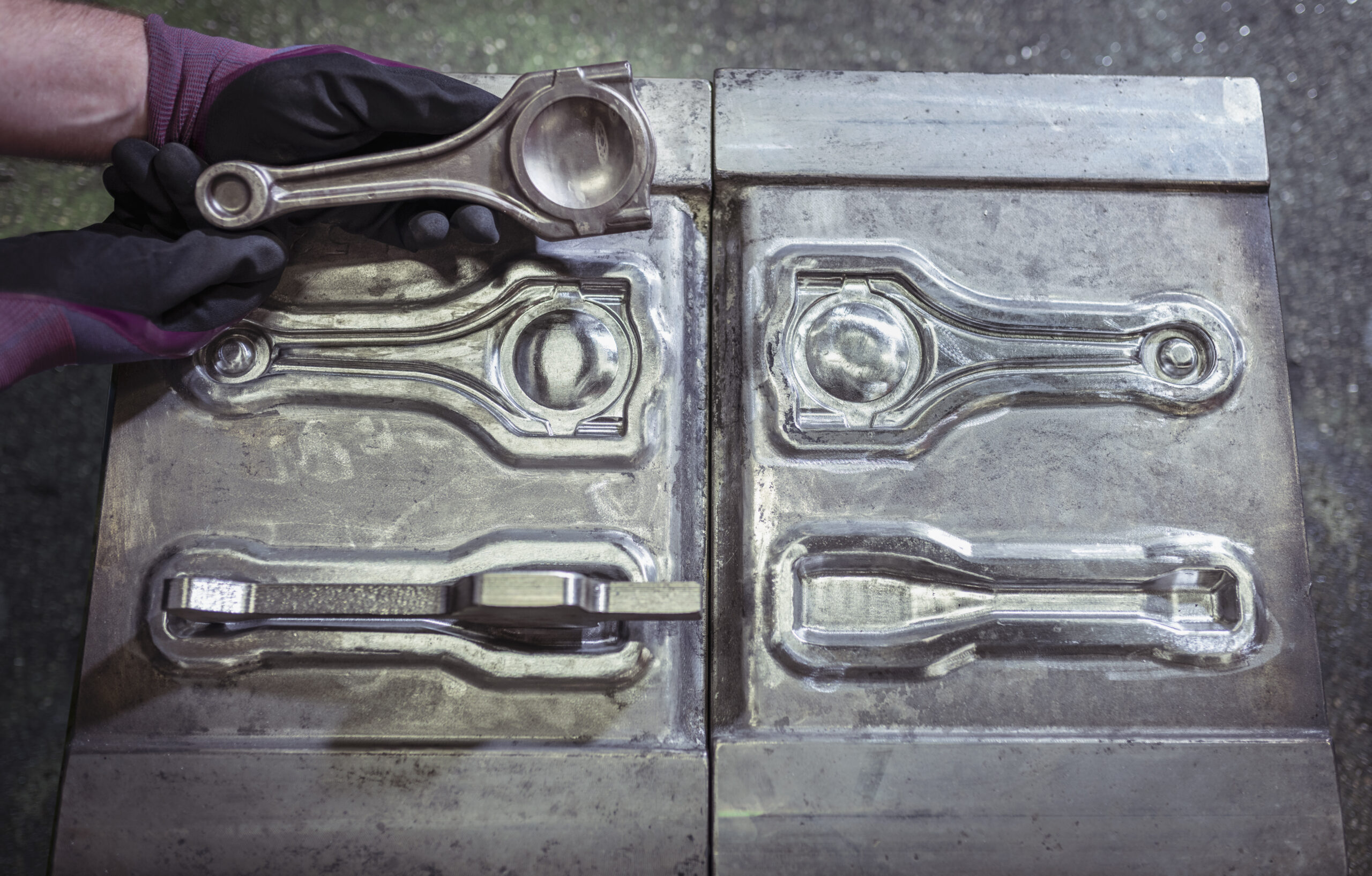
The process of mold design and creation
Mold design and creation are fundamental steps in the casting process, playing a critical role in determining the quality and functionality of the final product. A well-designed mold ensures that molten metal flows evenly, solidifies properly, and meets the desired specifications without defects. Whether it’s for aluminum casting or other types of metals, the precision in mold design significantly impacts the efficiency and cost-effectiveness of the manufacturing process.
1.Conceptual design: The mold design process begins with understanding the requirements of the part to be cast. This includes considering factors like the metal to be used, the size and shape of the part, and the production volume. The design team uses this information to create a conceptual mold design that meets the technical specifications.
2.Simulation: Before the mold is physically created, simulations are often used to test its effectiveness. Advanced software allows engineers to simulate the casting process, predicting how molten metal will flow and solidify within the mold. This helps to identify potential issues, such as areas where the metal might cool too quickly or where air could become trapped, causing defects. Making adjustments in this virtual stage helps avoid costly mistakes later.
3.Prototype and testing: Once the design has been validated through simulations, a prototype mold may be created. This prototype is used for trial castings to ensure that it functions as expected. During this phase, any issues discovered during testing can be addressed by adjusting the mold design before moving into full production.
4.Final mold creation: After successful prototyping, the final mold is manufactured. Molds can be made from various materials, depending on the casting method and the type of metal being used. For example, permanent molds for aluminum casting are often made from steel, while molds for other metals may require specialized alloys or materials with specific thermal properties.
Benefits of proper mold design
1.Cost efficiency: A well-designed mold reduces the likelihood of defects and rework, leading to fewer wasted materials and faster production cycles. This increases the overall efficiency of the casting process, lowering manufacturing costs.
2.Improved product quality: Proper mold design results in higher-quality castings that meet specifications with minimal defects. This is particularly important in industries like automotive and aerospace, where the performance and safety of parts are critical.
3.Extended mold life: Molds that are designed with precision and made from durable materials can last longer, reducing the need for frequent replacements or repairs. This contributes to long-term cost savings and helps maintain consistent production quality.
4.Enhanced flexibility: Good mold design can accommodate various types of casting methods, including gravity casting, die casting, or sand casting, depending on the requirements of the product. This flexibility allows manufacturers to adapt to different production needs while maintaining quality.
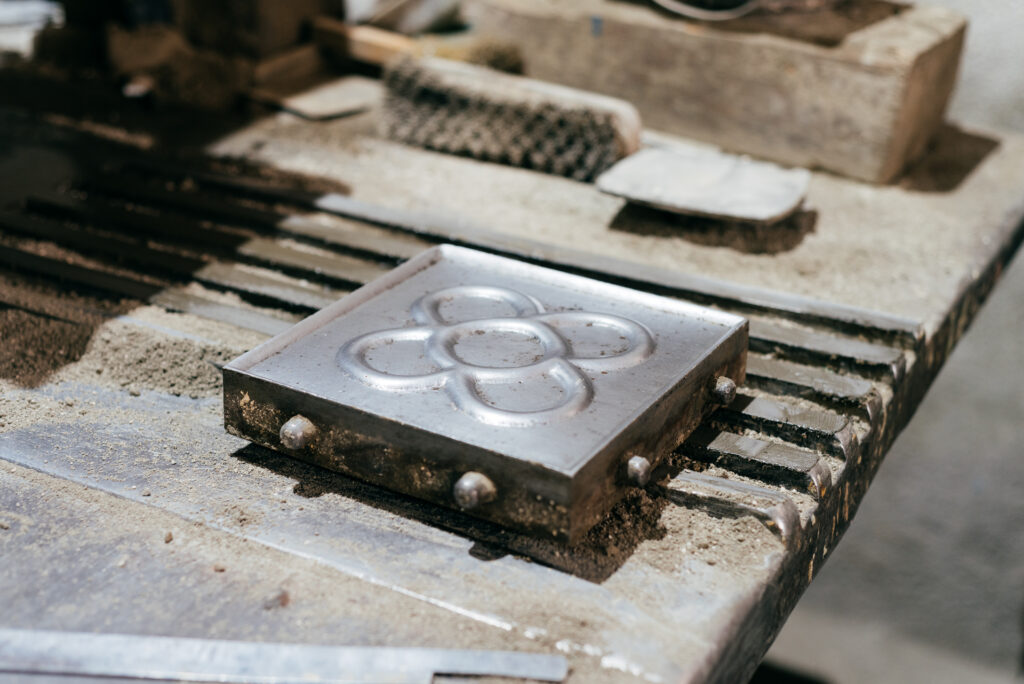
Conclusion
Mold design and creation are critical to the success of the casting process. By carefully designing molds and using simulations to refine their performance, manufacturers can optimize the flow and solidification of molten metal, reduce defects, and ensure that the final product meets the highest standards of quality. Investing in proper mold design not only improves the efficiency of the production process but also results in long-term cost savings and better-performing products.